Introduction
In solar power generation systems, combiner box are crucial links connecting solar panels to inverters. With their reliable current aggregation and distribution capabilities, rail-type combiner box provide essential technical support for the efficient operation of the entire system. This article will thoroughly analyze the installation procedures, special considerations, and long-term maintenance strategies for rail-type combiner boxes to ensure that devices remain in optimal condition and have an extended lifespan.
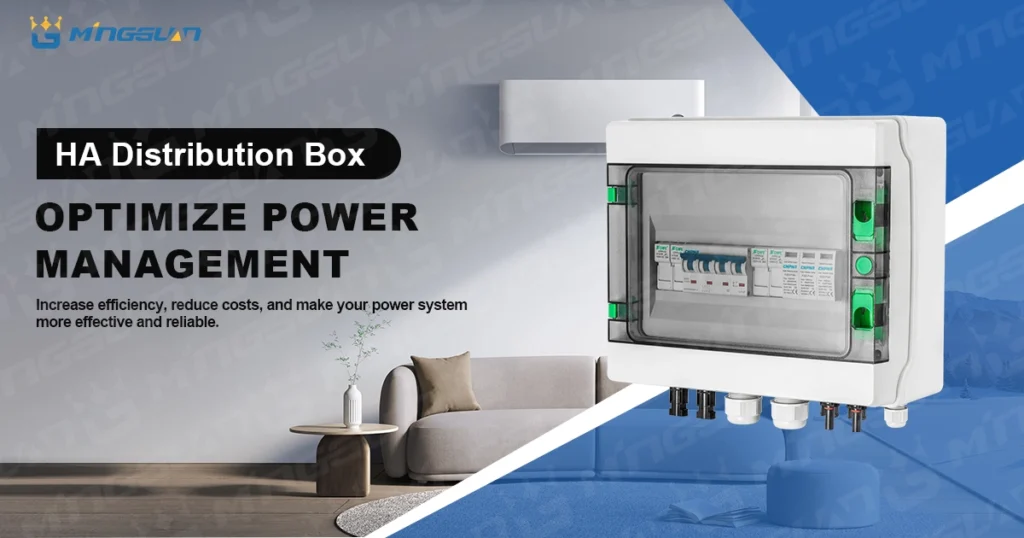
1. The Role and Importance of Rail-Type combiner box
Rail-type combiner box play a central role in solar power systems. These devices not only aggregate the direct current produced by multiple photovoltaic components but also safely transmit it to one or more inverters. Additionally, combiner box play a crucial role in protecting circuits and regulating current.
Functionality of combiner box:
The functionality of combiner box can be broken down into several essential components:
- Current Aggregation: combiner box ensure that the total power output from multiple solar panels is gathered efficiently. This is vital for optimizing energy transfer to the inverter.
- Protection Mechanisms: Many combiner box are equipped with protective mechanisms such as fuses or circuit breakers, safeguarding the electrical components from overcurrent and short circuits.
- Surge Protection: Some models include built-in surge protection devices to shield the system from voltage spikes and surges, which can be caused by lightning strikes or grid fluctuations.
- Ease of Maintenance: Robust design and modular build make it easier for technicians to conduct maintenance and repairs when necessary, increasing the longevity of the solar power system.
The selection of an appropriate combiner box, along with correct installation and maintenance, is the key to ensuring high efficiency, reliability, and low failure rates of photovoltaic systems.
2. Preparations Before Installation
Equipment and Tool Checklist
Before starting the installation, ensure that all necessary tools and equipment are prepared. This includes electrical tools (such as torque wrenches, voltage testers, and cable strippers), protective gear (such as insulated gloves, safety goggles, and hard hats), and product manuals for reference.
Typical Equipment List:
- Solar panel connectors
- Wrench set for mounting hardware
- – Screwdrivers (flathead and Phillips)
- Cable ties for proper cable management
- Level for ensuring proper alignment
- Measuring tape for precise installations
- Multimeter for testing electrical connections
- Cleaning materials (for maintenance)
Environmental Assessment and Position Selection
Choosing the installation location is vital. The ideal installation site should be away from flammable gases or chemical storage areas, and there should be enough space to guarantee adequate ventilation and maintenance convenience.
Considerations for Site Selection:
- Accessibility: Ensure that the installation area is easily accessible for routine maintenance and emergency responses.
- Sun Exposure:Choose a location that provides maximum sunlight exposure while avoiding shading from trees or buildings.
- Temperature Control: Areas with extreme temperatures or humidity should be taken into account, using weather-resistant materials as necessary.
3. Installation Steps for combiner box
1. Fixing the Rail
- After identifying the position, securely attach the rail to the wall or mounting bracket using high-strength expansion bolts or appropriate clamps. Use a level to ensure both horizontal and vertical accuracy. If using a wall-mounted rail system, ensure that the wall material can support the rail’s weight, especially when multiple panels are connected.
2. Mounting the combiner box on the Rail
- Carefully hang the combiner box on the installed rail. Due to the sliding groove design of the rail, ensure that the combiner box fits snugly without becoming loose or misaligned. Utilize the handbook for guidance on properly adjusting the box to the rail.
- After secure installation, check the stability of all fastening points again and make adjustments as necessary for proper stability. This prevents movement during operation, which could strain electrical connections.
3. Electrical Connections
- The electrical connections of the combiner box require great precision. First, ensure that the connections of the solar panels’ positive and negative terminals are accurate; each connection port should be firmly crimped to avoid poor contact.
- Use a torque wrench to adhere to specified torque settings for cable lugs and connections to prevent under-tightening or over-tightening that could lead to wear or damage.
- The conductor size should be chosen according to the current rating of the combiner box, and the cable length should be reasonable to minimize voltage loss. If longer cable runs are required, consider using larger gauge wire to maintain efficiency.
4. Grounding and Safety Protection
- Safety protection is a critical step in electrical installation. The combiner box should have a comprehensive grounding system, connecting a separate ground wire to the grounding system to prevent damage from static electricity or lightning strikes. Ensure that grounding connections are clean and free from corrosion.
- Grounding should follow local electrical codes. A grounding plate or rod may be necessary based on local regulations and environmental conditions. Confirm that all grounding procedures are correctly documented.
5. Powering Up the System and Preliminary Testing
- Once all connections have been confirmed as correct, the system can be powered on for preliminary testing. Use voltage measurements at each connection point to confirm that the input and output values are within the design range.
- Perform functional testing, verifying the operation of protective devices and ensuring that the system behaves as expected under load conditions. Record these tests for future reference.
4. Installation Considerations
Safety and Protection of Personnel
- All installation operations should strictly adhere to safety production regulations. Wear personal protective equipment, such as insulated gloves, protective clothing, and safety goggles, to effectively reduce the risk of accidents.
Compliance with Electrical Standards
- Local electrical installation standards may vary, especially regarding cable torque tension, insulation treatment, and grounding wire safety requirements. It is essential to familiarize yourself with these regulations to avoid non-compliance issues.
Device Labeling and Cable Management Standards
- Equipment installations should be clearly labeled, and cable management should be organized to ensure neatness, using high-temperature, UV-resistant ties for securing cables. This facilitates easier troubleshooting and maintenance down the line.
Environmental Suitability
- Installation should take into account environmental climate conditions, selecting cables and connectors suitable for extreme temperatures and humidity fluctuations. Additionally, consider the possibility of wildlife interactions and install barriers if necessary.
5. Daily Maintenance Requirements for combiner box
1. Regular Inspections and Documentation
- Proactive regular inspections can help prevent significant failures. Record device operating time, alarm information, and current readings. Additionally, check the integrity of the outer shell for any signs of cracks, sealing for waterproofness, and the tightness of all connections.
Inspection Checklist:
- Physical condition: look for any visible damage or wear.
- Electrical connections: check for signs of overheating or corrosion.
- Sealing and enclosure: ensure all seals are intact and effective.
- Surge protective devices: evaluate their condition based on visual signs of damage.
2. Cleaning Procedures
- Although combiner box are typically designed to be sealed, external contaminants can still affect their performance. Regularly clean dust and dirt from the exterior and check ventilation openings to ensure optimal heat dissipation.
- Use soft cloths or brushes—avoid abrasive materials that could damage the box surface.
3. Electrical Performance Testing
- Regularly measure the current, voltage, and temperature of each module to confirm that devices are operating optimally. This can help identify any deviations that may indicate fault conditions.
- If performance declines or any abnormal noise is detected during operation, the system should be shut down to troubleshoot, checking for damaged connections or wiring. Use a multimeter to measure voltage drop across connections and identify any resistive issues.
4. Optimization and Upgrades
- Regular technological updates and equipment upgrades can continually improve system efficiency. As new technologies emerge in the solar industry, consider upgrading components that may enhance system performance.
- Periodically evaluate system performance against current standards and technology. If new sensors or monitoring systems are available, assess whether integrating them can lead to better operational insights and efficiencies.
5. Response to Emergencies
- Define emergency response measures for combiner box failures and related electrical devices, establishing a maintenance management protocol and emergency contact system to ensure prompt handling of unexpected situations.
- Train personnel in emergency protocol, ensuring they are familiar with disconnection techniques and safety measures in the event of an electrical fault.
6. Common Issues and Solutions
1.Cable Aging and Breakage
- Cables exposed to harsh environments over long periods may age and require regular replacement. Implementing cable management practices can effectively reduce the risk of faulty connections and cable breaks.
- Use weather-resistant cables rated for outdoor use, and consider encapsulating critical connections in protective sheathing.
2.Thermal Management Issues
- During peak loads, devices may overheat. Consider factors that influence combiner box temperature, including ambient temperature, airflow, and the thermal conductivity of materials.
- Adding heat sinks or improving airflow around the combiner box can help solve these problems. Additionally, avoid placing equipment in direct sunlight for extended periods, as excessive heat can lead to premature component failure.
3.Abnormal Current or Circuit Breaks
- Frequent activation of circuit protection may indicate loose connections or excessively high capacitance. Conduct thorough inspections to spot corrosion or physical damage and ensure that all components function correctly.
- Utilize preventative maintenance schedules to periodically tighten connections and check terminal blocks for wear.
3.Moisture Ingress
- If moisture is detected inside the combiner box, inspect seals and gaskets for integrity. Ensure that the box is mounted in a location away from potential sources of water accumulation, and use conformal coatings where applicable.
7. Evolution of Technology in combiner box
As technology evolves, combiner box are becoming smarter and more capable. Innovations such as remote monitoring and integrated metering systems allow for real-time performance analysis and quick response to issues. These tools enable operators to make informed decisions about maintenance needs and can even automate fault detection and tracking.
- Smart combiner box:
- A trend among manufacturers has been the development of smart combiner box equipped with IoT (Internet of Things) technology. These systems can communicate data about performance metrics to a centralized monitoring system.
- The benefits of smart combiner box include:
- Enhanced monitoring: Provides real-time data on system performance, enabling rapid response to anomalies or declines in output.
- Proactive maintenance alerts: Sends notifications when maintenance is needed or when performance metrics exceed thresholds.
- Integration capabilities: Can interface with various monitoring and control systems, streamlining energy management processes.
Conclusion
As a core component of photovoltaic systems, the installation and maintenance of rail-type combiner box directly impact the performance and safety of the entire power system. Through careful attention to installation steps, diligent daily inspections, and timely maintenance, users can effectively ensure stable, long-lasting operation while reducing maintenance costs.
In the ever-evolving landscape of energy technology, proactively updating and upgrading devices provides a safeguard for continued high-efficiency operation. By implementing sound technical practices, the potential for maximizing the economic and environmental benefits of renewable energy can be achieved.
The detailed guide discussed here emphasizes the importance of optimizing the performance of rail-type combiner box, covering technical tips, compliance guidelines, and strategies to address potential issues. This information is beneficial not just for engineering professionals but also for participants in the solar energy sector by providing clear best practices for installation and maintenance.
In conclusion, as solar technology advances, the role of combiner box will become even more integral in ensuring efficient, safe, and sustainable energy production. By adhering to best practices in installation and maintenance, stakeholders can derive maximum value from their solar power systems, contributing positively to both their energy needs and the environment.