In recent years, with the global energy structure transformation and the promotion of carbon neutrality goals, photovoltaic power generation, as an important component of clean energy, has achieved remarkable development speed. The key components of photovoltaic systems, such as photovoltaic panels and inverters, often receive much attention. Although pv connectors are small in size and have a low cost proportion, they play a crucial role in the operational reliability and cost control of the entire system. This article systematically analyzes how to reduce the total cost of solar power generation systems by optimizing the design of pv connectors from the perspectives of cost composition, system cost impact, and optimization design.
This article systematically explores the cost composition of PV connectors, their impact on overall system costs, and strategies to optimize their design to enhance performance and reduce costs. By addressing these factors, we can better understand how to improve the long-term economic and operational viability of PV systems.
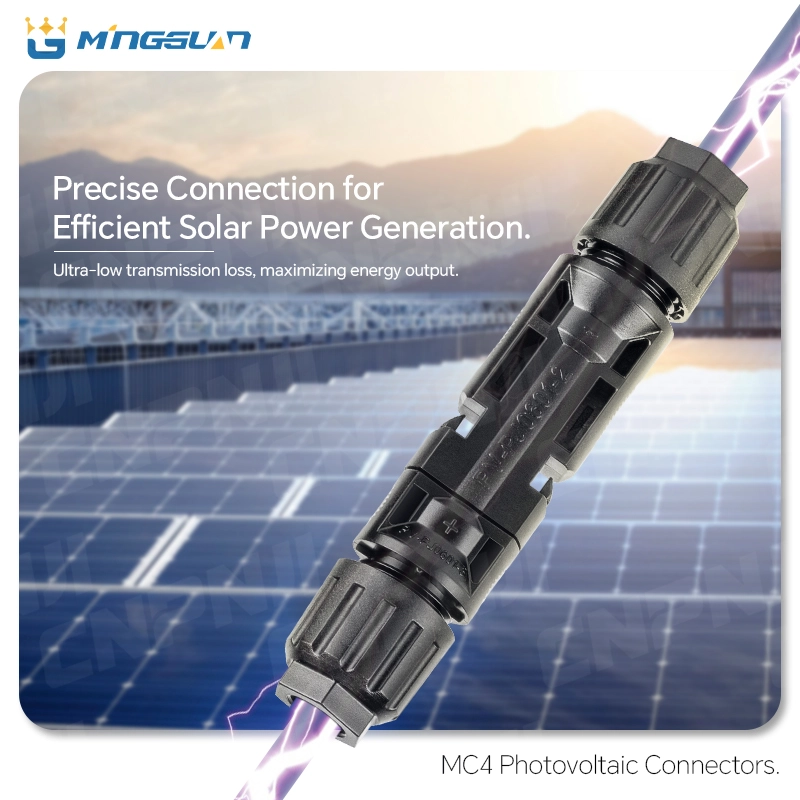
1. The Role and Importance of PV Connectors
1.1 Functions of PV Connectors in PV Systems
PV connectors are small yet indispensable components in PV systems. They serve as the interface between PV modules, direct current (DC) cables, and other critical equipment. Their main functions include:
1. Electrical Connection: PV connectors ensure efficient and stable transmission of electrical current from the solar panels to the inverter. This is achieved with minimal resistance and minimal energy loss, which is crucial for optimizing system performance.
2. Safety Protection: These connectors provide insulation, waterproofing, and dustproofing, protecting the system from external environmental factors such as humidity, dust, ultraviolet (UV) radiation, and corrosion. Their role in maintaining electrical safety and preventing potential short circuits or fires cannot be overstated.
3. Modular Installation: Through their standardized designs and quick plug-and-play mechanisms, PV connectors simplify on-site installation and maintenance. This reduces the complexity and time required for system setup, making them invaluable for large-scale solar farms and residential systems alike.
By fulfilling these roles, PV connectors play a pivotal part in ensuring the reliability, efficiency, and safety of the entire PV system. For example, high-quality connectors reduce contact resistance, which enhances energy efficiency and reduces power losses. Additionally, their ability to withstand harsh environmental conditions over prolonged periods ensures system durability and cost-effectiveness.
1.2 Assessing the Value of PV Connectors
Although PV connectors typically account for less than 5% of a PV system’s total cost, their value extends far beyond their price tag. Industry studies have revealed that approximately 15%-20% of PV system failures are caused by connector-related issues. These failures can disrupt power generation and, in some cases, lead to catastrophic consequences such as electrical fires.
Substandard connectors can also compromise the overall efficiency of the system by increasing power losses or requiring frequent maintenance and replacement. As such, investing in reliable, high-quality connectors is essential to maximizing the long-term benefits of PV systems.
2. Cost Composition of PV Connectors
Understanding the cost structure of PV connectors is critical for identifying opportunities to optimize their design and reduce expenses. The primary cost components are as follows:
2.1 Material Costs
– Conductive Core: Copper is the most commonly used material for the conductive core due to its excellent electrical conductivity. However, in some high-performance connectors, silver-plated copper is used to further reduce contact resistance. While effective, these materials can significantly increase the overall cost of the connectors.
– Insulation and Housing: The connector housing is typically made from weather-resistant plastics such as polycarbonate (PC) or polyamide (PA). These materials must offer high resistance to UV radiation, temperature fluctuations, and aging while maintaining sufficient mechanical strength to protect the internal components.
2.2 Manufacturing Costs
– Tooling and Injection Molding: Producing high-precision molds for connector components requires significant upfront investment, particularly for complex designs. The injection molding process must also ensure tight tolerances to maintain performance standards.
– Assembly and Testing: Each connector must undergo rigorous assembly and testing processes to ensure it meets strict electrical, mechanical, and environmental standards.
2.3 Certification Costs
PV connectors must comply with international standards such as UL, TUV, and IEC to gain market access. Certification involves extensive testing to verify electrical safety, thermal performance, and environmental durability, which adds to the overall cost.
2.4 Logistics and Packaging Costs
Due to their small size and delicate construction, PV connectors require protective packaging and careful handling during transportation. These measures help prevent damage and ensure the connectors reach their destination in optimal condition.
2.5 Research and Development (R&D) Costs
Manufacturers continually invest in R&D to develop innovative designs, improve performance, and reduce costs. These efforts are particularly important for meeting the evolving demands of the PV industry, such as higher efficiency and longer lifespans.
2.6 Maintenance and Replacement Costs
Low-quality connectors often fail prematurely, necessitating frequent replacements and increasing operation and maintenance (O&M) costs. Over the lifespan of a PV system, these costs can accumulate significantly, making it critical to prioritize durability and reliability in connector design.
3. Impact of PV Connectors on System Costs
Although PV connectors represent a small portion of a system’s equipment costs, they have an outsized influence on installation, operation, and maintenance costs. Their performance and reliability also affect the system’s overall energy efficiency and return on investment.
3.1 Installation Costs
The installation phase typically accounts for 20%-30% of a PV system’s total cost. By incorporating modular and standardized designs, PV connectors can streamline the installation process and reduce labor requirements. For example, quick plug-in mechanisms allow for faster assembly and fewer wiring errors, which are particularly beneficial in large-scale solar farms.
According to industry data, improving connector design can reduce installation costs by 5%-10%, saving millions of yuan in large projects. This is especially important as labor costs continue to rise globally.
3.2 Energy Loss
Power loss due to high contact resistance in connectors can have a significant impact on system performance. For instance, a 100MW PV plant could lose hundreds of thousands of yuan annually if its connectors are not optimized. Reducing contact resistance by 1% can increase energy efficiency by 0.2%-0.5%, making high-quality connectors a worthwhile investment.
3.3 Operation and Maintenance Costs
Reliable connectors reduce the need for frequent maintenance by preventing issues such as loosening, corrosion, or overheating. Faulty connectors, on the other hand, can cause system downtime, leading to lost revenue and increased repair expenses. By investing in durable connectors, operators can minimize O&M costs and ensure uninterrupted power generation.
4. Optimization Strategies to Reduce PV Connector Costs
Reducing the cost of PV connectors requires a multi-faceted approach that includes material innovation, structural optimization, and process improvements. The following strategies have proven effective:
4.1 Material Optimization
1. Conductive Core Materials:
– Copper-Aluminum Composites: Replacing part of the copper core with aluminum can lower material costs while maintaining adequate conductivity.
– Silver Plating Optimization: Reducing the thickness of silver plating can balance cost and performance.
2. Insulation and Housing Materials:
– Developing new UV-resistant and weatherproof polymers can reduce material costs without compromising durability.
4.2 Structural Optimization
1. Integrated Design: Combining multiple functional components into a single housing reduces manufacturing complexity and costs.
2. Quick Plug-In Mechanisms: Improved plug and socket designs enhance contact stability, simplify installation, and minimize errors.
3. Lightweight Design: Reducing material usage lowers costs and simplifies logistics while maintaining performance.
4.3 Automated Manufacturing
1. Robotic Assembly: Automated production lines improve precision and efficiency, reducing labor costs and defect rates.
2. Quality Inspection Automation: Advanced inspection systems ensure consistent product quality while reducing reliance on manual checks.
4.4 Enhanced Environmental Adaptability
1. Corrosion Resistance: Improved materials and coatings enhance performance in high-humidity or coastal environments.
2. Sealing Technology: Achieving higher waterproof ratings (e.g., IP68) extends connector lifespan and reduces maintenance requirements.
4.5 Intelligent Features
1. Embedded Sensors: Real-time monitoring of temperature, current, and voltage can help detect faults early, minimizing downtime and repair costs.
2. IoT Connectivity: Remote monitoring and diagnostics enable proactive maintenance and reduce the risk of unexpected failures.
5. Economic Impact of Optimized Connector Design
5.1 Cost Reduction Potential
Optimized designs can reduce the production cost of PV connectors by 15%-20%. For instance, a 100MW PV system that spends 3 million yuan on connectors could save up to 600,000 yuan through improved designs. Additional benefits, such as enhanced energy efficiency and reduced maintenance costs, further boost the system’s profitability.
5.2 Impact on Levelized Cost of Energy (LCOE)
The levelized cost of energy (LCOE) is a critical metric for evaluating the competitiveness of PV systems. By lowering connector costs and improving efficiency, LCOE reductions of 0.01-0.02 yuan per kWh are achievable. These savings are particularly significant for large-scale projects where small cost reductions can translate into substantial financial gains.
6. Conclusion
While often overlooked, PV connectors are integral to the success of solar power systems. Their design and performance have a profound impact on installation efficiency, energy output, and maintenance costs. By adopting innovative materials, streamlining manufacturing processes, and integrating intelligent features, manufacturers can significantly reduce connector costs while improving system reliability and efficiency.
As the PV industry continues to grow, the importance of connectors will only increase. Future advancements in modularity, durability, and smart technology will further enhance their value, contributing to the widespread adoption.